肥料工业发展的基本出发点是保证我国农业的可持续发展、粮食安全和生态环保。当前,我国化肥产业面临的主要问题是: 产能过剩,投入多、产出少,资源消耗高,生态环境问题较为突出; 产品结构不能完全适应农业发展的需要,更不适应企业自身做大做强的需要。今后复混肥的发展应落实到加快技术进步、提升工艺装备技术水平,生产满足作物需要的测土配方肥、缓释肥、水溶性肥料、有机- 无机肥等; 加快节能降耗新工艺研究和产业化工作; 积极开发低能耗、低污染的肥料新品种,提高肥料利用率,实现产品、技术的升级换代,提高产品竞争力。因此,研发优质、高效、安全、生态环保的肥料工艺技术和产品是“十二五”期间磷复肥工业技术领域创新发展的重要方向。
目前,高塔复混肥虽然解决了传统复混( 合)肥氮含量不高的难题,但是在生产低氮、高磷产品上有着自身的限制。国内的高塔尿基复混肥产品大多属于高氮( N≥20%,质量分数,下同) 低磷( P2O5≤12%,质量分数,下同) 系列,原因在于低氮( N < 20%) 高磷( P2O5≥12%) 系列熔体料浆黏度较大、流动性差,频繁堵塞管道、喷头,开车率低,产品质量不稳定。而大田作物拔节期对于磷( P2O5) 的要求一般在15%左右,部分农作物及经济作物需求N-P2O5-K2O 为18-18-18,17-17-17,16-16-16, 15-15-15 的尿氯基复混肥、17-17-17 的尿硫基复混肥、16-16-16 的硝氯基复混肥、15-15-15 的硝硫基复混肥、水溶性肥料等。
近几年来,为提升工艺技术水平、延伸产业链、调整产品结构、提高产品质量及生产能力、降低生产成本、提高产品竞争力,在借鉴相关高塔复混肥装置技改经验基础上,通过生产摸索、技术攻关、技术研发及技术升级改造,逐步完善了高塔熔体造粒法复混肥工艺及其装备技术,形成了1 套新的技术创新体系,实现了产品、技术的升级换代,开发了低能耗、低污染的清洁生产工艺。
优化升级改造前的工艺流程
原高塔造粒复混肥生产工艺由熔融、粉体配料、粉体加热、制浆、造粒、筛分、防结块、计量包装、堆包码垛等工序组成,其工艺流程如图1 所示。
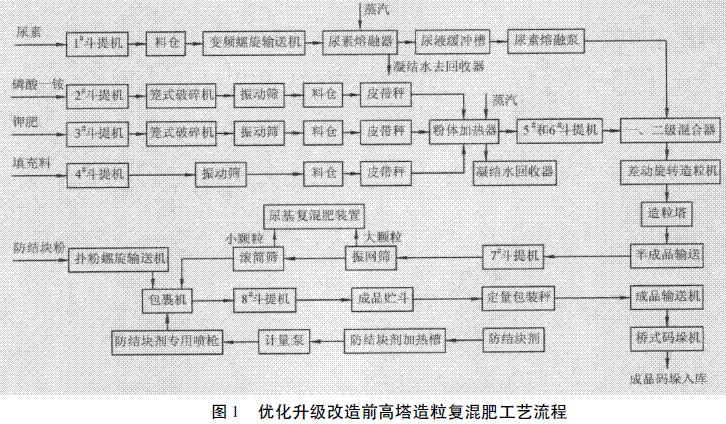
来自原料库的颗粒尿素经人工拆包后倒入地坑皮带受料口,由地坑皮带及斗提机输送至尿素料仓,经变频给料螺旋输送机进入尿素熔融器,熔融后的尿素流入尿液缓冲槽,由尿素熔融泵输送至塔顶一级混合器,与来自粉体加热工序的粉体物料混合; 氯化钾或硫酸钾、磷酸一铵、填充料分别经人工拆包后倒入地坑皮带受料口,由地坑皮带及斗提机输送至笼式破碎机破碎( 无块粒状物料可不经破碎) ,粉体物料经振动筛筛分进入料仓,料仓底部设电子皮带秤,分别计量后经混合皮带送入粉体加热器加热及预混合; 加热混合后的粉体物料经粉体皮带输送机、5# 和6# 斗提机输送至制浆工序的粉体料仓,然后经电子皮带秤进入一级混合器,与来自尿素熔融工序的尿液搅拌混合; 混合后的料浆溢流入二级混合器进行剪切分散混合,然后溢流入差动旋转造粒机将熔体料浆喷入造粒塔内; 经喷头喷撒出的小液滴在下降过程中与上升的空气流进行传质、传热,落至塔底冷却固化成球状颗粒( 半成品) ,由刮料机刮入塔底皮带机,经皮带送入半成品斗提机( 7# ) ; 半成品再经7#斗提机提升至振网筛及滚筒筛进行筛分,筛分后的少量大颗粒和小颗粒分别经计量包装后转运至尿基车间原料库,由尿基车间再进行加工制成复混肥料。
粉体配料加热工序、制浆造粒工序及成品筛分工序抽出的含尘气体经旋风除尘器、沉降室除尘后,达标的尾气经排气筒放空。